Examine This Report about Alcast Company
Table of ContentsThe Definitive Guide to Alcast CompanyExcitement About Alcast CompanyA Biased View of Alcast CompanyAlcast Company Fundamentals ExplainedNot known Incorrect Statements About Alcast Company The Greatest Guide To Alcast Company
The subtle difference depends on the chemical content. Chemical Comparison of Cast Light weight aluminum Alloys Silicon advertises castability by decreasing the alloy's melting temperature level and boosting fluidness throughout spreading. It plays a vital function in enabling detailed molds to be filled accurately. Additionally, silicon adds to the alloy's stamina and wear resistance, making it valuable in applications where sturdiness is critical, such as automotive parts and engine elements.It also enhances the machinability of the alloy, making it easier to refine right into completed products. In this means, iron adds to the total workability of light weight aluminum alloys.
Manganese contributes to the toughness of aluminum alloys and boosts workability. Magnesium is a lightweight aspect that offers toughness and effect resistance to aluminum alloys.
All about Alcast Company
It permits the production of light-weight parts with superb mechanical homes. Zinc improves the castability of light weight aluminum alloys and helps regulate the solidification procedure throughout spreading. It boosts the alloy's strength and hardness. It is usually found in applications where complex forms and fine details are required, such as ornamental spreadings and certain automobile parts.
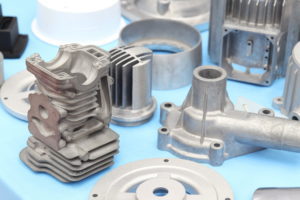
The main thermal conductivity, tensile toughness, yield stamina, and prolongation vary. Select ideal resources according to the efficiency of the target item produced. Among the above alloys, A356 has the highest possible thermal conductivity, and A380 and ADC12 have the most affordable. The tensile limitation is the contrary. A360 has the very best yield toughness and the highest elongation price.
Everything about Alcast Company

In precision spreading, 6063 is well-suited for applications where complex geometries and top notch surface coatings are paramount. Instances consist of telecommunication enclosures, where the alloy's exceptional formability enables streamlined and visually pleasing styles while maintaining structural honesty. Likewise, in the Illumination Solutions sector, precision-cast 6063 parts produce sophisticated and reliable illumination fixtures that require complex shapes and good thermal performance.
The A360 shows superior prolongation, making it suitable for complicated and thin-walled components. In precision casting applications, A360 is well-suited for markets such as Customer Electronic Devices, Telecommunication, and Power Devices.
What Does Alcast Company Mean?
Its unique residential properties make A360 an important selection for accuracy spreading in these sectors, enhancing item toughness and top quality. aluminum foundry. Aluminum alloy 380, or A380, is a commonly made use of casting alloy with several distinctive qualities.
In precision casting, aluminum 413 shines in the Consumer Electronics and Power Tools industries. Check This Out This alloy's superior rust resistance makes it an exceptional choice for exterior applications, making certain long-lasting, resilient products in the pointed out industries.
8 Simple Techniques For Alcast Company
The aluminum alloy you pick will substantially affect both the spreading procedure and the buildings of the final item. Because of this, you need to make your choice meticulously and take an educated strategy.
Figuring out the most suitable light weight aluminum alloy for your application will certainly suggest weighing a vast variety of characteristics. The very first category addresses alloy features that influence the production procedure.
The Single Strategy To Use For Alcast Company
The alloy you select for die casting directly affects a number of facets of the spreading process, like just how very easy the alloy is to deal with and if it is vulnerable to casting flaws. Hot cracking, also understood as solidification fracturing, is a common die casting problem for light weight aluminum alloys that can cause inner or surface-level tears or fractures.
Specific aluminum alloys are extra at risk to hot cracking than others, and your choice needs to consider this. It can damage both the actors and the die, so you need to look for alloys with high anti-soldering residential properties.
Deterioration resistance, which is currently a remarkable attribute of light weight aluminum, can differ significantly from alloy to alloy and is a necessary characteristic to consider depending upon the ecological problems your item will certainly be subjected to (aluminum casting manufacturer). Use resistance is an additional property typically looked for in light weight aluminum products and can differentiate some alloys